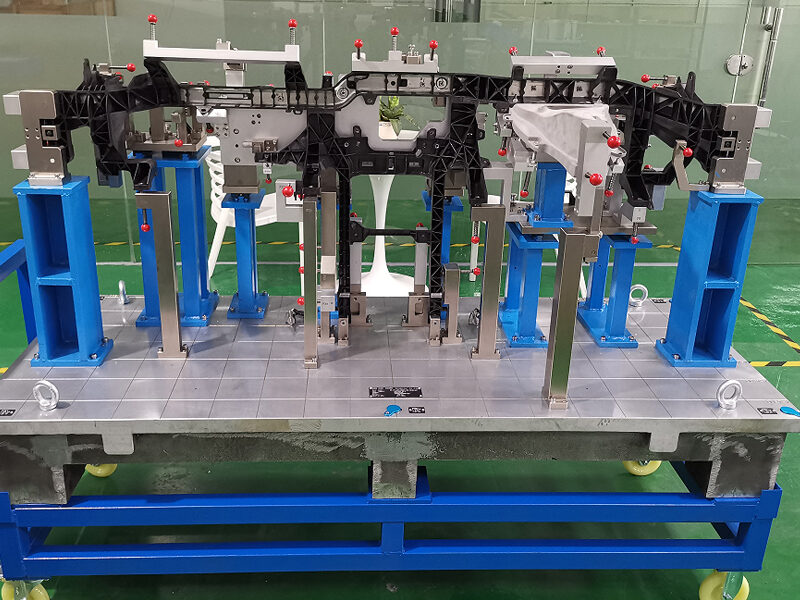
Application and development of carbon fiber automotive check fixtures
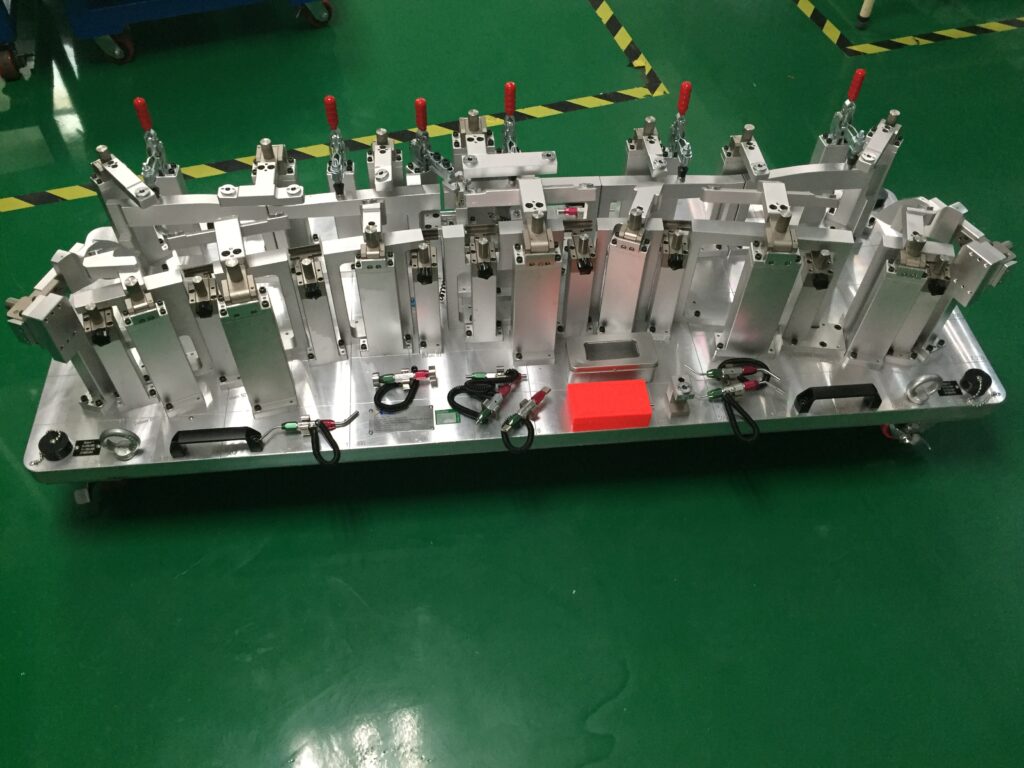
At present, there are more cases of applying carbon fiber composite materials in automotive check fixtures, especially for portable hand-held check fixtures such as front windshield frame, door frame and luggage compartment frame, the lighter the weight of the check fixtures, the better, for example, the front windshield opening check fixtures, in the past, the aluminum tube skeleton plus resin simulation block, so that the weight of a check fixture is about 30KG, but due to the limited strength of the aluminum tube, once the use of high evaluation rate, the aluminum tube skeleton will The use of carbon fiber composite materials to produce this checker, the total weight of only 10-15KG, and long service life, can effectively ensure the accuracy of the checker test, some large car manufacturers for the use of carbon fiber materials to reduce the weight of this aspect also attaches considerable importance, such as Shanghai GM has been actively on the checker itself to optimize and upgrade the material. For example, Shanghai GM has been actively optimizing and upgrading the material of the check fixture itself, from the initial resin opening check fixture for the front and rear lights of 618 models to the E12 full carbon front and rear windshield opening check fixture, and now it is developing from carbon fiber skeleton plus resin simulation block to full carbon fiber one-piece check fixture.
The degree of application of carbon fiber composites in different types of automotive fixtures varies, and the achieved lightweight effect is also different, but the actual application effect is still very satisfactory, for example, a carbon fiber automotive lamp check fixture, the check fixture uses a carbon fiber body with the same shape as the automotive lamp, the carbon fiber body is provided with a positioning module near the side face of the automotive lamp, and a threaded sleeve is provided at the rigid positioning module, where The carbon fiber material used as the body of the check fixture is only 5mm thick to meet the strength requirements, light in mass and small in deformation, and at the same time can simulate the whole lamp surface and have a better appearance.
There are many kinds of automotive check fixtures, and the design of different models for each brand also has large differences and personalization, in practice, bulky is the common problem of check fixtures, by using carbon fiber composite material tubes, plates and structural parts instead of structural steel parts, can greatly reduce the weight of the check fixtures, to avoid thin-walled parts easily deformed by pressure, and further improve the accuracy of measurement, but from the current stage of market development and application However, from the current stage of market development and application, the problems of carbon fiber automotive check fixtures are also very obvious
One is to clarify the purpose of the application of carbon fiber composite materials, the design of the automotive check fixture itself is quite complex, to achieve the integration of carbon fiber check fixture for the molding process of carbon fiber composite materials, not only in technology is a huge challenge, but also will largely push up the application cost, but will hinder the application of carbon fiber materials in the check fixture, check fixture developers can use carbon fiber composite materials instead of the check fixture in the Crossbeams, brackets and other non-positioning pieces of ordinary steel structural parts, it can achieve the purpose of weight reduction, so that the cost can also be controlled accordingly.
Second, in the process of using carbon fiber composite materials instead of metal structural parts, we should pay attention to the bonding of carbon fiber composite materials and the overall check fixture, simply put, the carbon fiber structure of the precise, solid bonding when the quality of the entire check fixture key, which not only requires high-strength epoxy resin to ensure the bonding strength, but also requires finishing links to enhance the interface bonding quality, in addition, the later CNC processing to determine the entire check fixture In addition, the later CNC machining determines the accuracy of the whole checker, and the professional tool and surface treatment have a great influence on the accuracy and surface quality of the checker.
In short, the use of carbon fiber composite materials for automotive check fixture lightweight effect is undoubtedly, but how to use to ensure the feasibility of cost and achieve the purpose of lightweight operation, the application of carbon fiber composite materials in automotive check fixture is an inevitable trend, but to cross the barriers still need to work hard.